In the competitive world of manufacturing, ensuring the longevity and reliability of machinery and products is often a direct result of the quality of components used. One such crucial component that plays an integral role in various industries is the high-quality rubber seal. Widely used in sectors ranging from automotive to aerospace, the demand for these seals underscores their importance in maintaining the efficiency and safety of equipment.
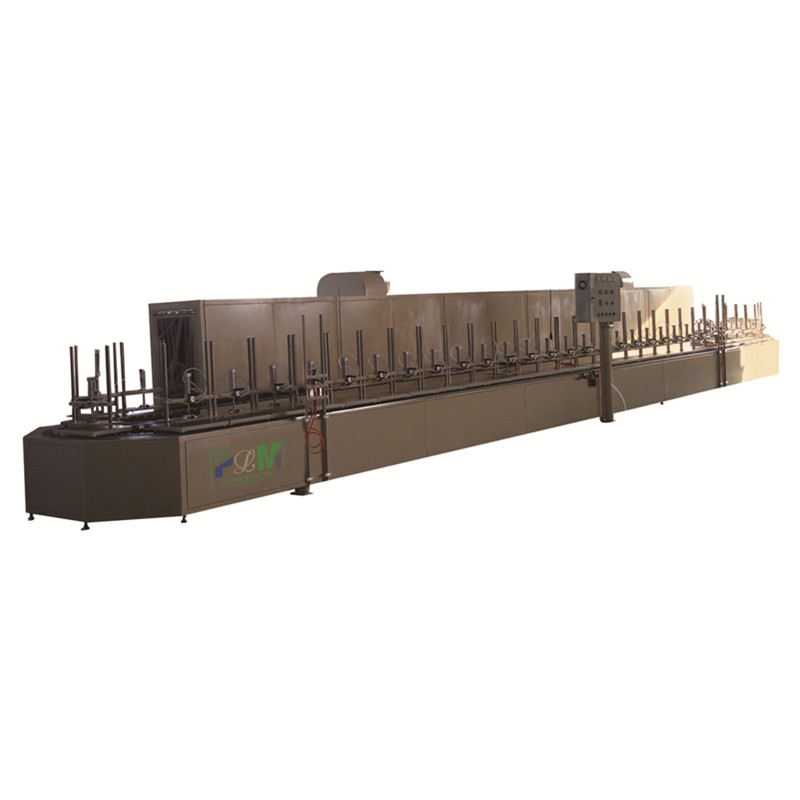
Understanding High-Quality Rubber Seals
Rubber seals are designed to prevent leaks between different substrate sections in both rotary and static settings. Their ability to mitigate the risk of fluid leakage makes them indispensable in engines, pumps, and other mechanical assemblies. High-quality rubber seals, however, transcend the basic expectations of preventing leaks; they ensure durability, compatibility with different chemical environments, and high-temperature endurance.
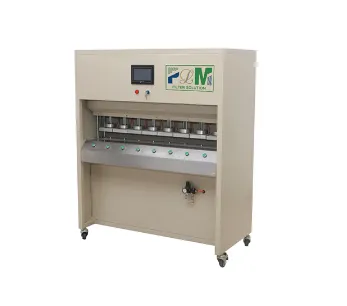
Durability A Defining Feature
One of the defining features of high-quality rubber seals is their unparalleled durability. They are crafted from advanced polymer technologies, often comprising materials such as silicone, nitrile, or EPDM (ethylene propylene diene monomer). Such materials are known for their resilience under stress and ability to sustain integrity over prolonged periods. Whether used in the harsh temperatures of a car engine or the chemical-rich environment of industrial applications, the durability of these seals minimizes maintenance costs, promising an economical choice for industries.
Compatibility with Chemical Environments
In specific sectors, like chemical manufacturing or oil and gas, rubber seals must resist an array of chemicals without degrading. High-quality rubber seals are engineered to withstand exposure to oils, acids, and other corrosive substances commonplace in these industries. EPDM seals, for instance, are particularly suitable for applications involving steam and hot water, given their outstanding chemical resistance. This versatility underlines their adaptability and is a testament to their meticulous engineering processes.
Temperature Resistance
In applications with extreme temperature variances, such as aerospace or automotive, the ability of a seal to maintain performance consistency is paramount.
High-quality rubber seals are designed to operate effectively across a spectrum of temperatures. Silicone seals, for example, are celebrated for their high-temperature tolerance without compromising elasticity or form. This temperature resilience ensures that even under the most challenging conditions, the seals will continue to operate efficiently, safeguarding the machinery and environment from potential failures.
high quality rubber seal
Craftsmanship and Precision
The craftsmanship involved in the production of high-quality rubber seals is a reflection of expertise and precision engineering. The manufacturing process involves stringent quality assurance practices to ensure that each seal meets the specific performance and dimensional criteria required by various applications. Precision tools and cutting-edge technology are utilized to guarantee that every seal adheres to the highest standards, underscoring the manufacturer's commitment to excellence.
Maintaining Industry Standards
High-quality rubber seals are typically in compliance with internationally recognized industry standards such as ISO, ASTM, and SAE. These standards serve as benchmarks for quality, ensuring that the seals not only fit the functional requirements but also meet safety and environmental considerations. Compliance with such standards assures stakeholders that the products are reliable and safe, which bolsters trust among consumers and manufacturers alike.
Expert Recommendations and Real-World Applications
For organizations unsure about the appropriate type of rubber seal to implement, consultation with experts is recommended. Professionals in the field can provide guidance based on the specific environmental conditions and requirements of the application. Real-world success stories and case studies further exemplify the efficiency and reliability of high-quality rubber seals. For example, a renowned automotive company successfully reduced engine failures by upgraded to a high-quality rubber seal that provided better heat resistance and longer service life, proving the tangible benefits of investing in quality components.
Building Trust Through Performance
The trust placed in high-quality rubber seals is ultimately built through consistent performance. Businesses and consumers alike can rely on their proven track record, which has been established through rigorous performance tests and validated in demanding environments. Such reliability means fewer downtimes, lower maintenance costs, and greater efficiency, which directly translate into better performance and profitability for industries that incorporate these essential components.
In conclusion, when selecting components for critical operations, opting for high-quality rubber seals is a strategic decision that underscores long-term efficiency and reliability. Their durability, chemical and temperature resilience, precise craftsmanship, and adherence to industry standards make them an authoritative and trustworthy choice across multiple sectors.