Selecting a high quality compressor air filter is a critical decision for maintaining an efficient and reliable pneumatic system. As industry professionals increasingly prioritize optimal performance and sustainability, the role of air filters cannot be overstated. The right filter not only ensures cleaner air but also extends the longevity of your machinery, reducing maintenance costs and minimizing downtime.
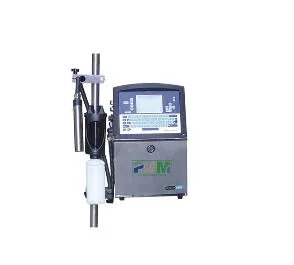
Understanding the nuances of different types of air filters enhances your ability to make informed decisions. There are primarily three main types particulate filters, coalescing filters, and vapor removal filters.
Particulate filters are designed to remove solid particles such as dust and pollen. These filters typically feature pleated designs to maximize surface area, thereby capturing larger volumes of particles. They are the most commonly used due to their effectiveness in a variety of environments.
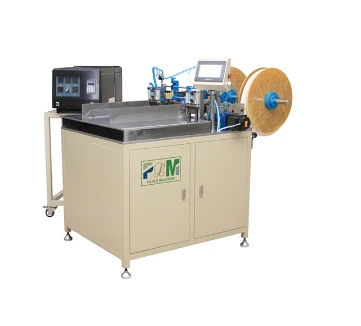
Coalescing filters, on the other hand, are used to remove water and oil aerosols from compressed air. These filters use a dense fiber or mesh material to capture and amalgamate liquid droplets until they are large enough to be drained or expelled. The key to their effectiveness lies in their ability to maintain low pressure drops while providing high levels of filtration.
Vapor removal filters, also known as activated carbon or charcoal filters, target gaseous pollutants such as oil vapor. They are crucial when the application requires the removal of smells or very fine oil mist particles.
Mechanical efficiency and adsorbent capacity are essential indicators of a high-quality compressor air filter in this category.
Experience from industry use suggests that the effectiveness of a compressor air filter is not solely dependent on its filtration medium or technology, but also on how well it is maintained. Regular inspections and timely replacements of filter elements are paramount. Neglecting maintenance can lead to increased energy consumption, frequent system failures, and contamination that could potentially harm sensitive equipment.
There’s an authoritative difference between a generic filter and a high-quality, brand-specific filter. Leading manufacturers dedicate extensive research into developing durable, efficient filters that meet industry standards and certifications. These filters often feature advanced materials and unique designs that offer superior filtration capabilities, thus earning trust from users worldwide.
high quality compressor air filter
Cost considerations should always be balanced against quality and effectiveness. While investing in a high-quality filter might seem costly upfront, the benefits of improved system efficiency, reduced energy consumption, and extended equipment life ultimately offer a more economical solution in the long term.
Expert technicians recommend selecting filters that adhere to International Organization for Standardization (ISO) classifications. This assures customers of a product that meets stringent quality standards. ISO 8573-12010, for example, outlines the purity classes of compressed air, emphasizing the importance of selecting filters that comply.
The trustworthiness of a supplier or manufacturer is another pivotal factor in choosing the right air filter. By dealing with reputable companies, you mitigate risks associated with subpar products that could fail under operating pressures or fail to comply with regulatory standards.
To achieve maximum efficiency, the correct sizing of a filter is crucial. An undersized filter may result in insufficient filtration, leading to contamination, while an oversized filter might lead to unnecessary pressure drops. Detailed analysis of operational pressures, temperatures, and flow rates informs the right fit for any given system and ensures longevity and effectiveness.
Future advancements in air filter technology promise to bring even more efficiency and cost savings. Innovations such as nanofiber filter media and smart filtration systems are poised to offer enhanced particle capture capabilities while allowing for predictive maintenance through real-time monitoring.
In summary, the selection of a high-quality compressor air filter involves a careful assessment of the system’s needs, understanding the types of contaminants present, and considering the environment in which the compressor operates. Combining this knowledge with insights from experienced professionals, authoritative certifications, and trustworthy manufacturers leads to a more effective and reliable filtration system. As technology progresses and the demand for cleaner air increases, industry leaders must continuously evaluate and adapt their filtration strategies to maintain an edge in the competitive landscape.