The Significance of Filter Plastic Mould Manufacturers in Modern Industry
In the intricate tapestry of modern manufacturing, filter plastic mould manufacturers play a crucial role. These specialized entities are responsible for crafting precision tools that shape the very components used in various industries to filter and purify fluids. The importance of their work extends beyond mere production; it influences environmental health, product quality, and even safety standards across different sectors.
The process of manufacturing filter plastic moulds is both an art and a science. It requires a deep understanding of materials science, engineering precision, and an eye for detail that can only be honed through years of experience. The manufacturers master the use of high-grade steel or aluminum to create cavities that, when filled with plastic, take on the exact shape needed for filtration elements.
These moulds must meet stringent requirements as they dictate the specifications of filters that safeguard against impurities in everything from drinking water to industrial fluids. A slight deviation in mould design can result in filters that fail to trap contaminants effectively, leading to potential health hazards or equipment malfunctions.
Technological advancements have significantly impacted the way filter plastic moulds are manufactured. Computer-aided design (CAD) software allows designers to visualize complex geometries and iterate designs with greater speed and accuracy Computer-aided design (CAD) software allows designers to visualize complex geometries and iterate designs with greater speed and accuracy
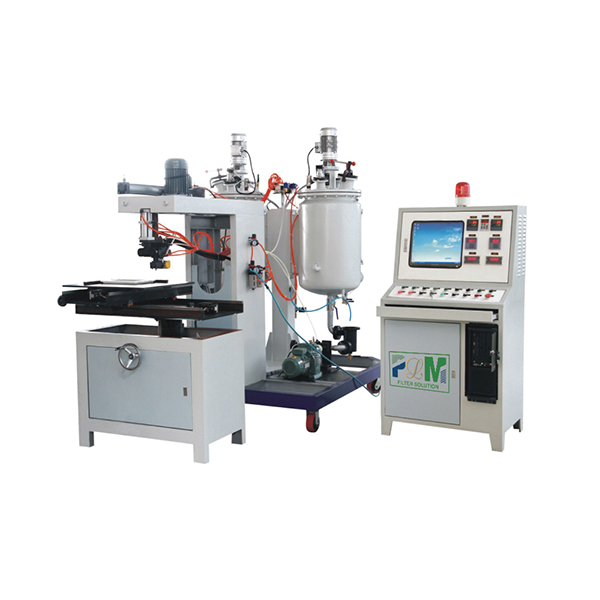
Computer-aided design (CAD) software allows designers to visualize complex geometries and iterate designs with greater speed and accuracy Computer-aided design (CAD) software allows designers to visualize complex geometries and iterate designs with greater speed and accuracy
filter plastic mould manufacturer. Computer-aided manufacturing (CAM) then translates these digital instructions into precise movements of cutting tools, ensuring each mould is created to exacting standards.
The sustainability aspect cannot be overlooked either. As global consciousness around eco-friendly practices increases, filter plastic mould manufacturers are under pressure to adopt more environmentally sound processes. This includes using recyclable materials and minimizing waste during production, aligning their operations with the green initiatives of their clientele.
In conclusion, filter plastic mould manufacturers stand at the vanguard of industrial innovation, upholding standards that protect our environments and products. Their commitment to precision, technology, and sustainability ensures that the filters we rely on daily continue to perform at peak efficiency. As we navigate an increasingly complex industrial landscape, these manufacturers are poised to adapt and evolve, continually shaping the future of filtration technology for generations to come.