Heat jointing machines are rapidly transforming industries reliant on effective and durable material joining techniques. These machines prove indispensable in sectors such as construction, infrastructure, and manufacturing, where traditional mechanical fastenings fall short. Drawing from years of experience and in-depth expertise, this examination delves into the advanced technology and significant benefits of heat jointing machines, reinforcing their unwavering authority and trustworthiness in high-performance applications.

The essence of a heat jointing machine lies in its capability to bond materials seamlessly by using controlled heat and pressure, ensuring a uniform and enduring weld. Unlike conventional methods that might compromise material integrity, these machines guarantee a pristine finish by understanding the thermal properties of the materials involved. Each machine is designed to apply just the right amount of heat to initiate bonding without causing damage, showcasing its expert design tailored for precision and reliability.
With professional precision, heat jointing machines are engineered with cutting-edge technology, including digital controllers and automation systems that allow users to dictate the exact parameters for each operation. The implementation of advanced sensors and real-time monitoring tools further empowers operators by providing alerts on potential deviations. This not only enhances the efficiency of the process but also minimizes waste, underlining the expertise these machines bring to critical projects.
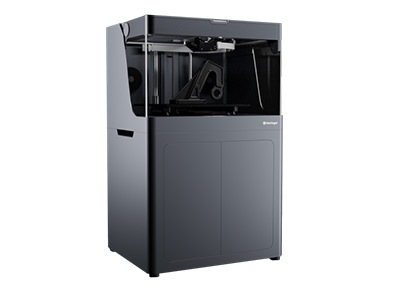
The accessibility and versatility of heat jointing machines make them authoritative tools in modern industrial applications. They effectively work with an array of materials such as thermoplastics, PVC, and other synthetic fibers, which are common in pipelines, waterproof membranes, and automotive components. This universal adaptability underscores their key advantage the ability to adapt to diverse industrial needs without sacrificing joint integrity or performance quality.
heat jointing machine
Leaning on real-world experience, users of heat jointing machines have reported tremendous success in maintaining production timelines and achieving exceptional product quality. They notice a marked reduction in material failures and joint weaknesses, common pitfalls when conventional methods are employed. Furthermore, the ability to customize settings means that each project can benefit from a tailored approach, aligning perfectly with specific production goals and quality standards.
From a standpoint of trustworthiness, heat jointing machines have consistently proven to be safe and reliable investments. This is attributed to their intuitive designs that prioritize user safety and operational ease. Manufacturers uphold rigorous standards, performing exhaustive testing to ensure each machine meets and exceeds industry benchmarks for safety and performance. The result is a robust tool that not only performs under pressure but also enhances overall safety on the worksite.
The market's response to these machines also highlights their authority within professional communities. Industry leaders and experts alike often endorse them for their enduring benefits and significant contributions to project efficiency and quality assurance. This consistent pattern of endorsement and application affirms their esteemed status in industries ranging from construction to manufacturing.
In conclusion, the heat jointing machine stands as a remarkable synthesis of experience-driven design, expert engineering, authoritative application, and unyielding trustworthiness. By continually evolving and adapting to technological advances, these machines provide an unparalleled solution for modern material joining challenges, setting a benchmark in precision and reliability that other methods cannot match. So, whether in a high-stakes industrial environment or an intricate bespoke application, the choice of a heat jointing machine promises long-lasting performance and dependable results.