In the dynamic world of manufacturing, the term plastic mould represents a pinnacle of technological advancement and precision. With the increasing demand for efficient, cost-effective production methods, plastic moulding has emerged as a cornerstone in various industries, from automotive to consumer electronics, medical devices, and beyond.
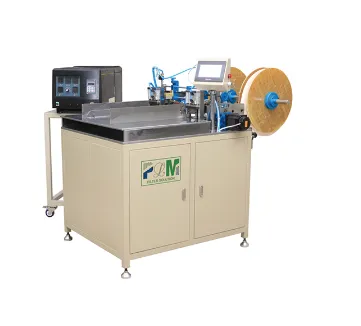
Plastic moulds are integral in the transformation of raw materials into finely crafted, dependable products that not only meet customer expectations but also adhere to stringent industry standards. A deep dive into the intricacies of this field reveals a blend of experience, expertise, authoritativeness, and trustworthiness—a quartet that forms the backbone of successful mould production.
Experience is a crucial component in crafting high-quality plastic moulds. Companies that have honed their processes over decades bring a wealth of knowledge and practical know-how to the table. Such firms understand the nuances of material selection, the subtleties of thermal expansion, and the precision required in mould cavity design. They leverage historical data and past projects to anticipate potential challenges and devise solutions that optimize the production process, reduce waste, and enhance the durability of the final product.
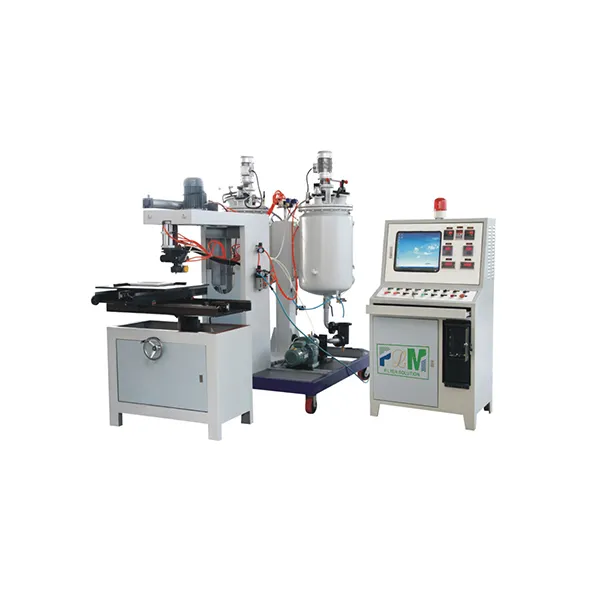
Expertise, on the other hand, is often demonstrated through a profound understanding of the latest technological advancements and methods in mould design and fabrication. Modern plastic moulding techniques employ sophisticated software for computer-aided design (CAD) and computer-aided manufacturing (CAM), allowing engineers to create detailed 3D models that facilitate precision engineering. Specialists in this field are adept at innovating designs that maximize efficiency, such as reducing cycle times and improving the cooling rate, which plays a critical role in determining the final product's structural integrity and aesthetic appeal.
Authoritativeness in the plastic mould industry is underscored by the meticulous adherence to international standards and regulatory requirements. Leading manufacturers often participate in shaping these standards, offering their insights and innovations as benchmarks for the industry. Their commitment to quality is reflected in certifications such as ISO 9001 for quality management systems, reinforcing their reputation as leaders and innovators in the field.
Trustworthiness is established through a consistent track record of delivering products that match client specifications and timelines. Reliable plastic mould producers are transparent in their operations, providing clients with clear timelines, realistic expectations, and open channels of communication throughout the moulding process. They also invest in quality assurance measures, employing rigorous testing protocols to ensure each mould meets the requisite safety and functionality criteria.
This level of transparency and reliability fosters long-term partnerships and client loyalty.
plastic mould
Within the realm of product innovation, the application of plastic moulding spans an array of industries, each with its unique set of requirements and challenges. In the automotive industry, for example, the development of lightweight, durable components is essential for enhancing fuel efficiency and vehicle performance. Here, plastic moulding facilitates the production of complex shapes and integrated parts that reduce assembly steps and improve joint reliability.
In the medical field, plastic moulds are pivotal in creating sterile, single-use devices that demand precision and compliance with health regulations. The expertise in creating moulds that can produce intricate, small-scale items ensures that medical professionals have the tools necessary for effective diagnosis and treatment.
Consumer electronics benefit significantly from plastic moulds as well. These devices require casings that provide both durability and aesthetic appeal, along with components that ensure accurate and reliable functionality. The capability to mould intricate geometries plays a vital role in the miniaturization trend prevalent in this sector, meeting consumer demand for compact, powerful devices.
Every industry reliant on plastic moulding exhibits a demand for innovation and precision. The companies that excel are those that invest in research and development, seeking out new materials and refining processes to push the boundaries of what's possible. Their continuous pursuit of excellence ensures that they maintain a competitive edge, driving their reputation as industry leaders.
In conclusion, plastic moulds are more than just tools of creation; they are a manifestation of deep-rooted experience, cutting-edge expertise, authoritative influence, and unwavering trustworthiness. In an era where the market demands both quality and efficiency, these moulding solutions stand as testaments to human ingenuity and dedication. Companies that master these facets not only thrive but also set the standards for others to follow.